Managing Noise, Dust & Air Quality in Demolition
Share this article:
Written by: Alpine Demolition
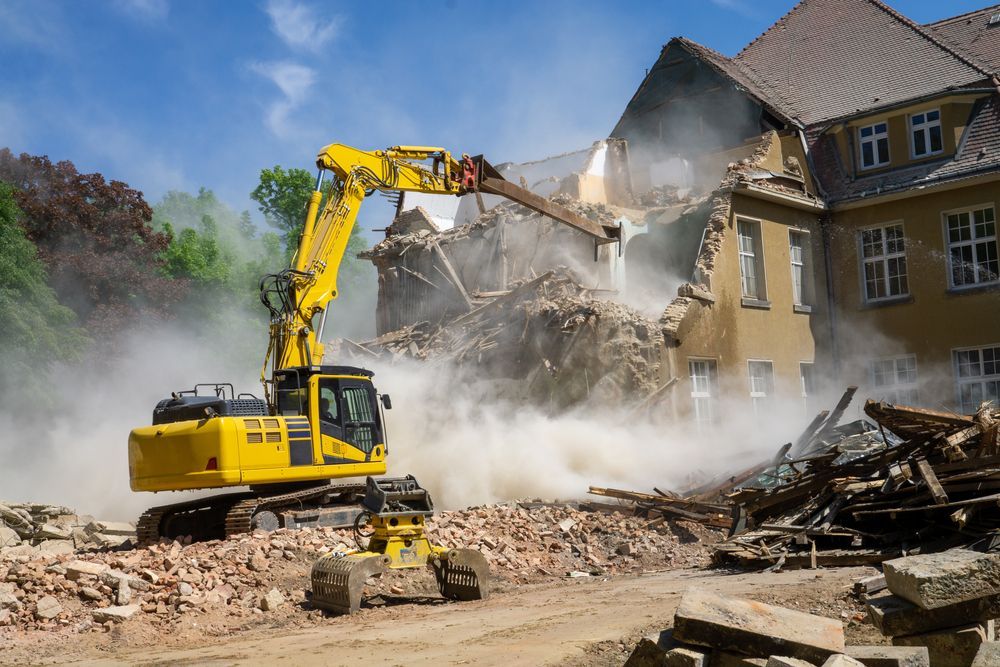
Demolition projects must do more than meet structural goals, they also need to minimize disruption to the surrounding environment. Controlling dust, reducing demolition noise, and protecting air quality are critical to maintaining safety, meeting regulations, and respecting the communities where work takes place.
Understanding the Environmental Impact of Demolition
Every demolition site generates a mix of airborne dust, elevated noise levels, and particulate emissions that can affect surrounding properties, businesses, and public spaces. Without proper safeguards, these impacts can compromise air quality in demolition zones and lead to enforcement actions or costly delays.
Dust control is especially important when removing materials that contain concrete, drywall, or insulation, which can release fine particles into the air. At the same time, demolition noise from machinery and structural collapse can exceed local thresholds and disrupt neighborhoods or commercial areas. Identifying these risks early allows project teams to develop mitigation strategies that protect people and minimize environmental disruption.
Planning for Noise, Dust, and Air Quality Control
Effective environmental control begins long before demolition equipment arrives on-site. A detailed plan is essential to address how noise, dust, and air quality will be managed throughout the project. This plan should account for local regulations, site-specific risks, and the proximity of sensitive receptors such as schools, hospitals, or residential areas.
Project teams conduct site assessments to determine prevailing wind patterns, nearby traffic, soil conditions, and building materials that may impact emissions or sound levels. From there, targeted solutions are integrated into the overall demolition strategy. This may include selecting specific equipment to reduce noise output, scheduling high-impact activities during less disruptive hours, or introducing active dust suppression systems. Early planning is the most reliable way to maintain control over air quality in demolition work and avoid costly surprises later in the schedule.
Best Practices for Dust Suppression on Job Sites
Dust control is one of the most important components of any demolition project, especially when working in close proximity to the public or other structures. Uncontrolled dust can affect visibility, create respiratory hazards, and contribute to regulatory violations if not properly managed.
Here are several best practices used to reduce dust on demolition sites:
- Water Suppression Systems:
Misting machines, hoses, and water trucks are commonly used to keep surfaces damp during demolition. Continuous water application binds dust particles, preventing them from becoming airborne.
- Pre-Wetting Structures:
Before mechanical demolition begins, pre-wetting the structure can reduce the initial surge of dust when walls or floors are broken apart. This is especially effective for concrete and masonry buildings.
- Enclosed or Covered Work Areas:
In areas with tight space or sensitive surroundings, temporary barriers or scaffolding covers can contain dust and keep it from drifting beyond the job site.
- Debris Handling Protocols:
Moving and loading debris slowly and from short drop heights helps reduce the amount of dust kicked up by material handling.
- Street Cleaning and Perimeter Control: Regularly sweeping access roads and installing gravel or tracking pads at exits keeps dust from leaving the site on vehicle tires or equipment.
Noise Mitigation Strategies in Urban and Suburban Areas
Managing demolition noise is essential when working near homes, schools, offices, or public infrastructure. Excessive sound levels can lead to complaints, delays, or even stop-work orders if not properly addressed. Every site requires a tailored approach to reduce the impact of noise while maintaining productivity.
Several strategies are commonly used to keep noise within acceptable limits:
- Equipment Selection:
Choosing modern, well-maintained equipment with low-decibel ratings can significantly reduce overall sound output. Some machines are specifically designed for quieter operation in sensitive environments.
- Work Hour Scheduling:
High-noise activities are often limited to daytime hours, avoiding early mornings, evenings, or weekends when disruption is most noticeable to surrounding communities.
- Sound Barriers and Acoustic Screens:
Temporary noise barriers can be installed around the perimeter of a job site to absorb or deflect sound, especially in areas close to residential buildings or pedestrian zones.
- Phased Demolition Plans:
Sequencing demolition work in smaller, controlled sections can help minimize peak noise levels and spread out the impact over time.
Proactive communication with nearby property owners and local officials also plays an important role. When communities know what to expect and when, they’re more likely to remain supportive throughout the project.
Air Quality Monitoring: Tools and Compliance Standards
Maintaining safe air quality in demolition projects requires both preventive measures and real-time monitoring. Tracking airborne particles helps identify when conditions exceed safe thresholds and allows crews to respond immediately. Monitoring is especially important in areas with vulnerable populations or strict environmental regulations.
Common tools and methods used on job sites include:
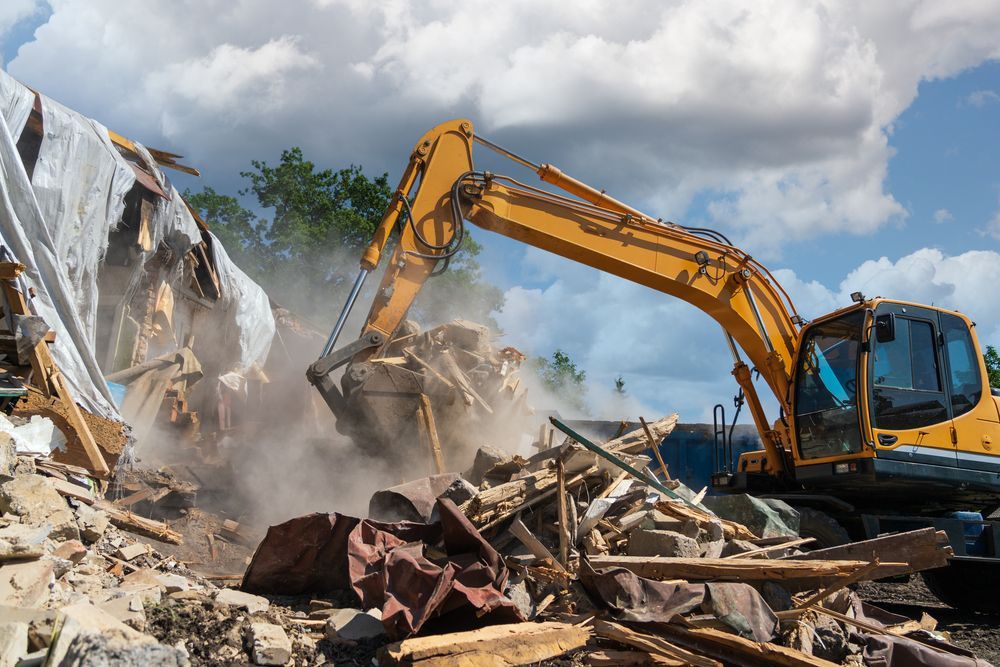
- Particulate Monitors (PM10 and PM2.5):
These devices measure the concentration of airborne dust and fine particles in real time. Monitoring helps confirm that dust control strategies are working and that levels remain within acceptable limits.
- Perimeter Air Sampling:
Air sampling stations are placed along the site boundaries to detect pollutants that may drift beyond the work zone. This helps contractors stay compliant with environmental standards and avoid violations.
- Visual Inspections and Logs:
While automated tools are valuable, trained crews also conduct regular visual inspections and keep records of dust-generating activities. These logs serve as both a compliance reference and a quality control tool.
- Data Reporting Tools: Digital platforms are often used to collect, track, and report air quality data to project managers, regulators, and clients. This transparency reinforces trust and demonstrates environmental responsibility.
Partnering with a Contractor Who Prioritizes Environmental Responsibility
Environmental concerns like dust control, demolition noise, and air quality should never be an afterthought. Choosing a contractor who understands how to manage these issues protects your project and your reputation.
Alpine Demolition takes a proactive approach to environmental responsibility, using smart planning and real-time monitoring to keep disruption to a minimum. Our team works closely with clients, city officials, and neighbors to ensure every project is handled with care and compliance.
If you're planning a demolition project and want a partner who takes environmental performance seriously, contact us or request a bid today.